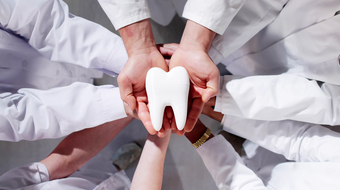
Stosowanie antybiotyków w leczeniu zakażeń zębopochodnych – kiedy jest naprawdę uzasadnione?
18.08.2025
Spersonalizowane implanty w technologii druku 3D
Nowoczesną drukarkę z certyfikatem medycznym wartości 400 tys. zł testują lekarze stomatolodzy z PUM w Szczecinie przy współpracy z inżynierami z Zachodniopomorskiego Uniwersytetu Technologicznego.
Drukarka medyczna została zakupiona z grantu aparaturowego pozyskanego przez dr n. med. Małgorzatę Tomasik z Zakładu Stomatologii Zintegrowanej PUM. Urządzenie jest już zainstalowane na Wydziale Inżynierii Mechanicznej i Mechatroniki ZUT. – Planujemy opracowanie metodyki wytwarzania spersonalizowanych implantów oraz podbudów protetycznych wytworzonych metodami przyrostowymi z materiału PEEK – mówi w rozmowie z podyplomie.pl prof. dr hab. n. med. Ewa Barbara Sobolewska z Katedry i Zakładu Protetyki Stomatologicznej PUM w Szczecinie.
Udział innowacyjnych technologii 3D w wykonywaniu implantów oznacza nie tylko wyższą jakość i dokładność wykonania względem metod tradycyjnych, ale również znaczne skrócenie czasu potrzebnego na jego wytworzenie.
Pierwszym etapem procesu wytwarzania implantów 3D jest stworzenie modelu uzębienia pacjenta za pomocą skanowania 3D bezpośredniego (laserowe skanowanie wewnątrzustne). Tak powstały model jest następnie przetwarzany w specjalistycznym oprogramowaniu, w wyniku czego określany jest dokładny kształt oraz lokalizacja przyszłego implantu. Zaprojektowany w ten sposób implant jest w pełni spersonalizowany zarówno pod kątem fizycznego dopasowania, jak i estetyki. W ramach końcowego etapu wirtualny model 3D implantu zębowego jest drukowany. To duży postęp w porównaniu ze stosowanymi obecnie powszechnie w implantologii gotowymi standardowymi implantami.
Tego typu systemy cyfrowe, choć są nowością, coraz odważniej wkraczają do gabinetów wypierając z nich tradycyjną metodę, polegającą na pobraniu wycisków z których technik następnie sporządza modele gipsowe, na których wykonuje nadbudowy protetyczne. Metody cyfrowe z pewnością zastąpią analogowe ze względu na ich znaczną precyzję .
- Nasza drukarka po raz pierwszy do wydrukowania implantów wykorzystuje materiał polieteroeteroketon (PEEK) –doskonale imitujący kość. W przeciwieństwie do stosowanych dotychczas materiałów, elastyczność PEEK jest zbliżona do elastyczności kości ludzkich – klasa D2. Sprawdził się on już w ortopedii, obecnie próbujemy go wdrażać w implantoprotetyce. PEEK nie był do tej pory wykorzystywany z użyciem technik przyrostowych (druk 3D)
Liczymy na to, że wykonane z niego uzupełnienia pozbawione będą wad, jakie mają popularne implanty tytanowe. Ze względu na sztywność implantu tytanowego i brak więzadeł ozębnej, po kilku latach powstają u pacjentów dolegliwości ze strony mięśni i stawów skroniowo-żuchwowych. Mamy nadzieję, że nasze nowe implanty ze względu na swoją elastyczność pozwolą uchronić pacjentów przed dolegliwościami – mówi prof. Ewa Barbara Sobolewska.
Obecnie metoda jest na etapie badań in vitro. Wykorzystując mikroskopy konfokalne naukowcy wykonują ocenę struktury geometrii powierzchni materiału wydrukowanych implantów. Powierzchnia zostanie wygładzona w technologii laserowej. Ważne jest, aby nie była ona chropowata i nie powodowała przylegania płytki nazębnej – tłumaczy prof. Sobolewska.
Jak zaznacza naukowczyni, badania są na wczesnym etapie, ostatecznych wyników jeszcze nie ma. W jej ocenie jest kwestią kilku miesięcy, kiedy rozpoczną się zabiegi z udziałem pacjentów.